Men's Indoor Soccer Cleats and Clothing
(23 Results)Time Out
You can select up to 3 products

BRASIL SALA ELITE TF - Futsal Shoe - Specific sole for synthetic surfaces - Men

BRASIL SALA ELITE ID - Futsal Shoe - Specific sole for indoor or parquet surfaces - Men

BRASIL SALA ELITE ID - Futsal Shoe - Specific sole for indoor or parquet surfaces - Men
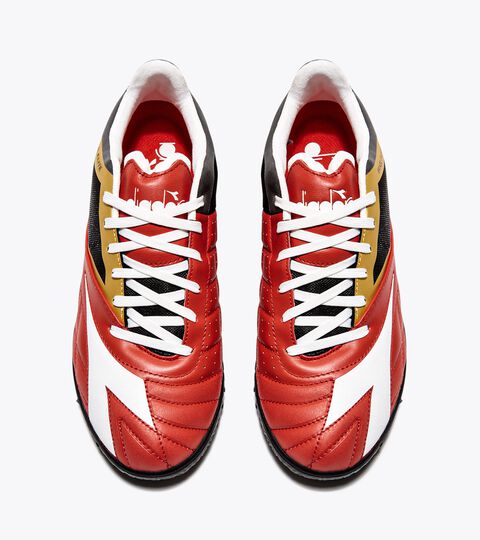
BRASIL SALA ELITE TF - Futsal Shoe - Specific sole for synthetic surfaces - Men

BRASIL SALA CUP ID - Futsal boots - Specific outsole for indoor grounds - Men
CALCETTO GR LT ID - Futsal boot - Specific outsole for indoor grounds
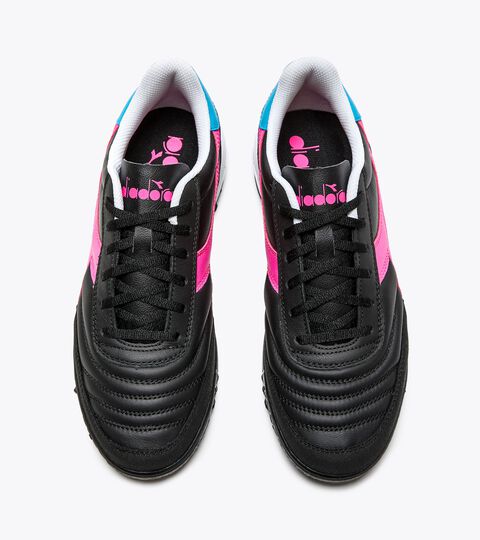
CALCETTO GR LT TF - Futsal boots for synthetic grounds - Men
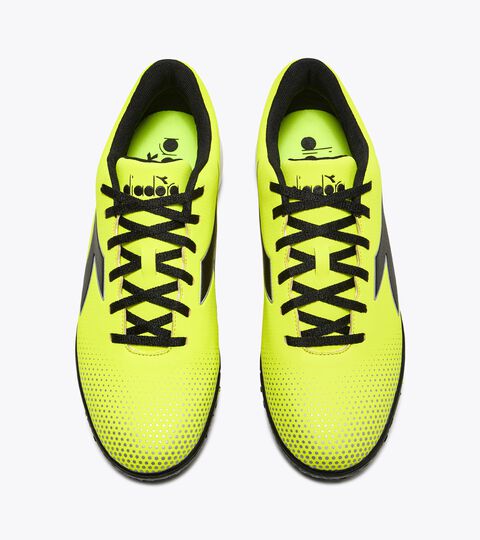
PICHICHI 7 TFR - Calcio boots for synthetic grounds - Men’s

BRASIL R TFR - Calcio boots for synthetic surfaces - All-Gender

PICHICHI 7 IDR - Indoor court calcio boots - Men’s
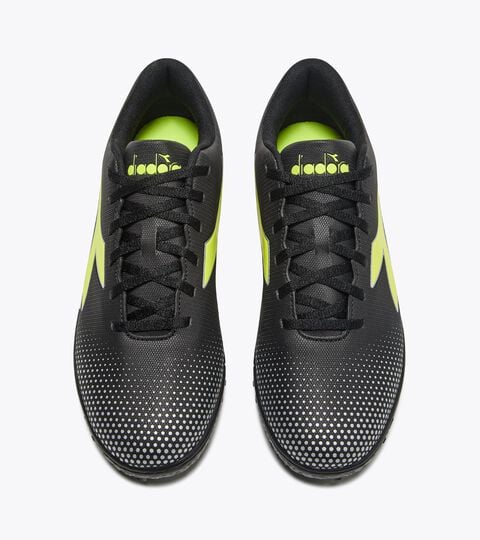
PICHICHI 7 TFR - Calcio boots for synthetic grounds - Men’s
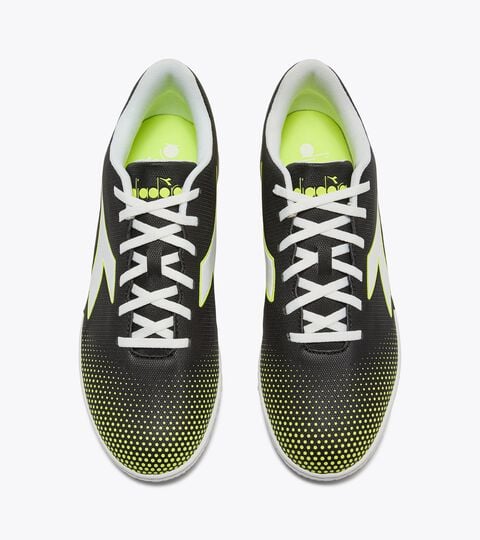
PICHICHI 7 TFR - Calcio boots for synthetic grounds - Men’s
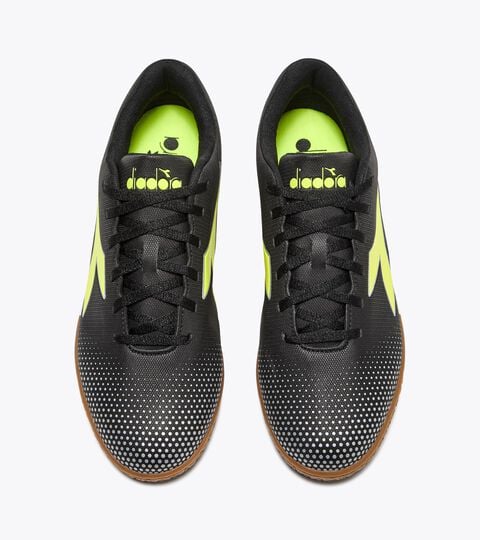
PICHICHI 7 IDR - Indoor court calcio boots - Men’s
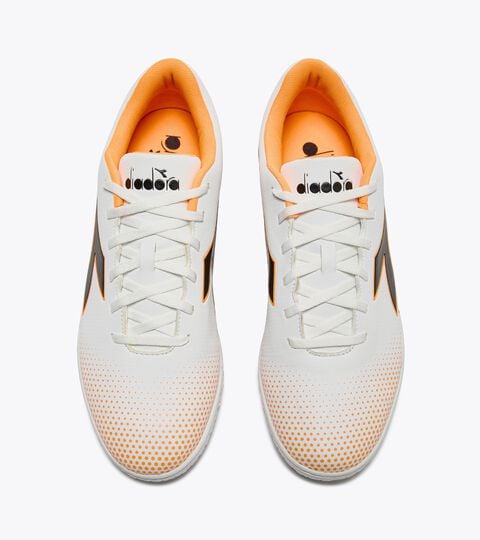
PICHICHI 7 TFR - Calcio boots for synthetic grounds - Men’s

BRASIL R TFR - Calcio boots for synthetic surfaces - All-Gender
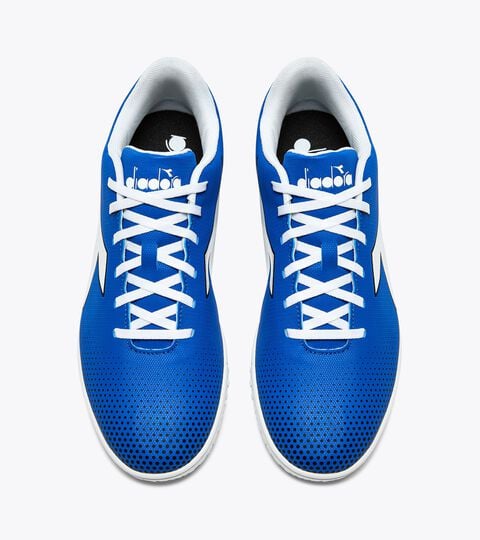
PICHICHI 7 TFR - Calcio boots for synthetic grounds - Men’s
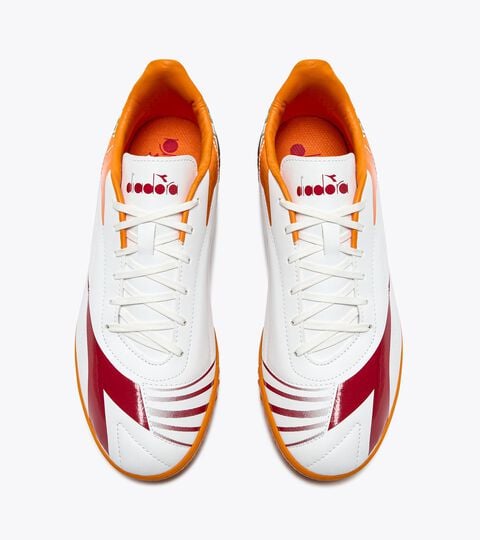
MAXIMUS ELITE R TFR - Calcio boots for synthetic turfs - Men’s

PICHICHI 7 IDR - Indoor court calcio boots - Men’s
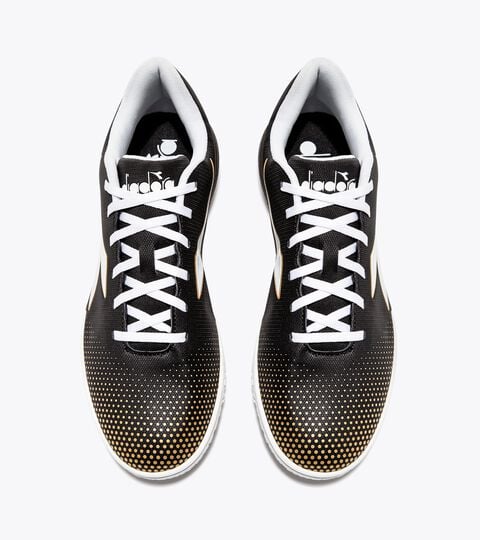
PICHICHI 7 TFR - Calcio boots for synthetic grounds - Men’s

PICHICHI 7 TFR - Calcio boots for synthetic grounds - Men’s
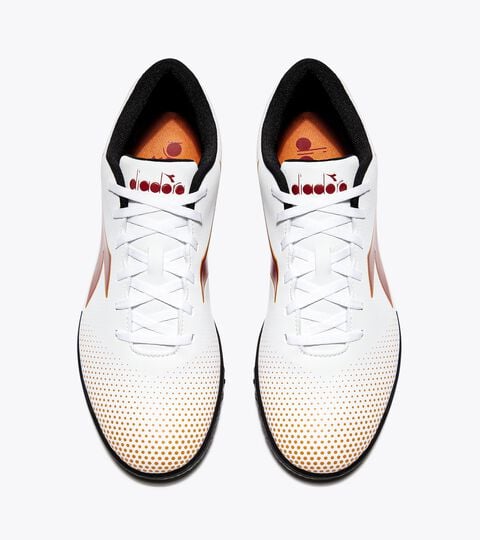
PICHICHI 7 TFR - Calcio boots for synthetic grounds - Men’s
Log in to your profile
Save your addresses and payment methods, review your orders and manage your wish list.
Or log in via
Join the Diadora Club
Register to discover all the advantages reserved for registered users:
Register